WHAT ARE GFRP REBARS?
GFRP stands for Glass Fiber Reinforced Polymer. It is a composite rebar,
which is a modern building material substituting the traditional metal Rebars.
GFRP Rebars consists of fibers of glass set in a resin matrix to form a rebar rod.
It is intended for reinforcing concrete structures which provide much more
durability with its excellent properties in which the rod has a spiral wound belt
extending above the core.
The first known usage of GFRP Rebars as a reinforcement was in the former
Soviet Union in the year of 1975.
GFRP Rebars major usage began in Europe in the 1980s which later gained
significant support during the 1990s from maglev-magnetically levitated
train support structures in Japan. Thus, the Japanese were the first to
introduce design guidelines for GFRP in reinforced concrete in the year 1996.
GFRP Rebars are 100% proven worldwide and are a corrosion prevention
product which has a widespread usage in countries such as USA, Canada,
Japan, Europe and Australia for more than 50 years.
Having various unique and proven characteristics, GFRP Rebars are widely
accepted in the construction industry worldwide and are one of the most
technologically and economical in application reinforcement.
ATTRIBUTES OF
GFRP REBARS
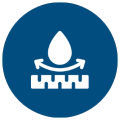
Corrosion Resistant
Prevents rust and damage from chemicals.
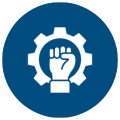
Stronger
Exceptional strength for heavy load handling.
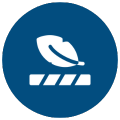
Lighter
Lightweight design ensures easy transportation.
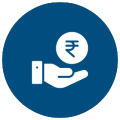
Zero Maintenance
Requires no upkeep for long-term use.
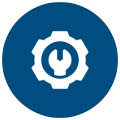
Eco Friendly
Environmentally safe and sustainable material.
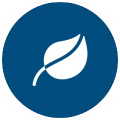
Cost Effective
High performance while reducing expenses.
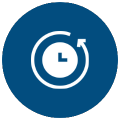
Longer Life Span
Outlasts traditional materials significantly.
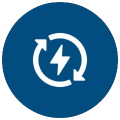
Dielectric
Non-conductive, safe for electrical applications.
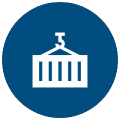
Easy to Transport
Lightweight and simple for logistical needs.
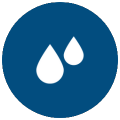
Less Thermal Expansion
Minimal size change under temperature shifts.
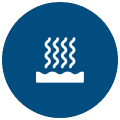
Radio Transparent
Unobstructed passage of radio signals.
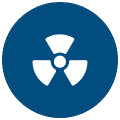
Water Resistant
Prevents damage from water exposure.
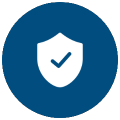
Lower Installation Cost
Reduces expenses during setup or assembly.
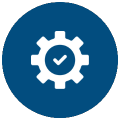
Easy to Handle
User-friendly and simple to modify onsite.
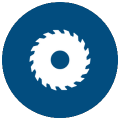
Durable
Strong, resilient, and damage-resistant.
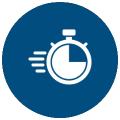
Fast, Safe Installation
Quick and risk-free installation process.
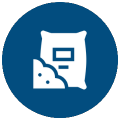
Less Concrete Coverage
Minimizes concrete usage for construction.
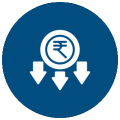
Reduced Overlap Costs
Lowers expenses on material overlapping.
Straight Rebar | Tensile Strength (MPA) | Ultimate Load (KN) | Tensile E-Modulus |
---|---|---|---|
8mm dia | 1000 | 50.27 | 50 |
10mm dia | 1000 | 78.55 | 50 |
12mm dia | 1000 | 113.11 | 50 |
16mm dia | 1000 | 201.1 | 50 |
20mm dia | 1000 | 314.2 | 50 |
22mm dia | 1000 | 380.1 | 50 |
25mm dia | 1000 | 490.9 | 50 |
28mm dia | 900 | 554.4 | 50 |
32mm dia | 900 | 723.6 | 50 |
34mm dia | 850 | 771.8 | 50 |
40mm dia | 850 | 1005.6 | 50 |
STANDARDS & DESIGN
GUIDES OF GFRP REBARS IN INDIA
2022
IRC: 137-2022
Guidelines on use of fibre-reinforced
polymer bars in road projects.
2023
IS 18255: 2023
Fibre-Reinforced Polymer (FRP) Rebars for
Concrete Reinforcement - Methods of Test.
IS 18256: 2023
Solid round glass fibre reinforced polymer (GFRP)
Rebars for Concrete Reinforcement - Specification
Testing Facility
We have an in-house testing laboratory and perform batch wise test reports as per Indian standards IS 18255:2023.
Testing Importance
Testing of GFRP Rebars is very important and crucial.
Couplers Requirement
GFRP Rebars are not tested the same way as we test metal rebars; in the case of GFRP Rebars, we must make couplers which act as grippers during testing. Testing of GFRP Rebars without the couplers acting as grippers is not possible as the bar may slip if put into the UTM (Universal Testing Machine) machine directly..